Vallum NDT ADR Machine
Advanced AI Solutions for Industrial Quality Control
- High Precision Detection: Advanced AI-powered system achieves over 95% accuracy in identifying surface defects
- Continuous Operation: Processes thousands of balls daily with 24/7 automated operation requiring minimal human intervention
- Cost-Efficient Solution: Replaces multiple manual inspection stations while significantly reducing labor and training costs
- Enhanced Safety: Enclosed UV lighting system eliminates operator exposure to harmful radiation during inspection
- Complete Coverage: Eight high-resolution images capture entire ball surface through sophisticated rotation mechanism
- Smart Analytics: User-friendly interface provides comprehensive statistical analysis and quality control tracking
- Non-Destructive Testing: Automated Defect Recognition (ADR) system ensures thorough inspection without damaging components
- Rapid Processing: Complete inspection cycle under 30 seconds enables high-throughput quality control
- Flexible Processing: Choice between local GPU-powered processing or cloud-based analysis for optimal deployment flexibility
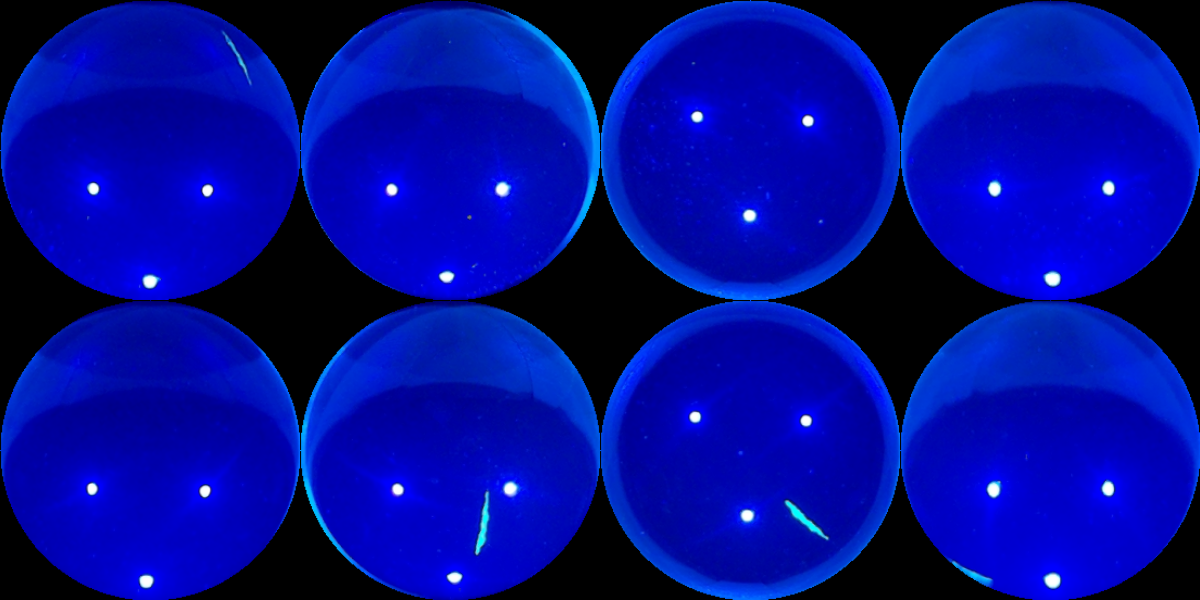
Comprehensive surface analysis: 8 high-resolution images capturing the complete surface of the ball for the AI-powered automatic defect recognition.
Product Overview
Our automated ball bearing inspection system revolutionizes quality control through seamless integration of robotics and AI technology. The process begins as balls are loaded into a feeding container, where they’re automatically queued and guided along a precision track. A proximity sensor monitors the track, ensuring optimal positioning of the mechanical blade that precisely feeds each ball into the inspection dome. Once inside, a second proximity sensor confirms the ball’s presence, triggering a specially designed claw mechanism that secures it in the perfect inspection position. The dome houses four high-resolution Raspberry Pi cameras and a sophisticated dual lighting system – UV lights for silicon nitride balls and white lights for steel balls. The system captures four detailed images of the upper hemisphere, then employs a precision wheel mechanism to rotate the ball 180 degrees for complete lower hemisphere imaging. These eight comprehensive images are processed either by a local GPU-equipped computer or sent to a cloud server for AI-powered defect analysis, offering flexible deployment options to suit different operational needs. Based on the analysis results, linear actuators guide each ball into separate channels for accepted or rejected components, maintaining a continuous flow of inspection with minimal human intervention and maximum accuracy.
Component Category | Specifications |
---|---|
Control System | • Raspberry Pi 5 |
Imaging Hardware | • 4x Raspberry Pi Camera v3 • Strategic 120° mounting configuration • Center-focused alignment |
Lighting System | • 3x UV LEDs (365nm, 5W) for Silicon Nitride Balls • 3x White LEDs (6500K) for Stainless Steel balls • 120° spacing configuration |
Motion Control | • 2x Pololu micro metal gearmotors • Nitride-hardened stainless steel gears • 3x 12V linear actuators |
Sensors | • 2x Proximity sensors • Track and calibrate feeding arm position • Dome center detection |
Mechanical Components | • Full 3D-printed housing • Precision ball-feeding blade • Precision ball positioning claw • Automated sorting channels |
Processing Capacity | • <30 seconds per ball • 2,000-3,000 balls daily • >95% detection accuracy |
Safety Features | • Enclosed UV lighting system • Automated handling system • Minimal operator intervention |
Processing Options | • Local processing: – NVIDIA GPU-equipped PC – Direct connection to device • Cloud processing: – Cloud-based model deployment – Remote processing capability – Network connection required |
For AI/ML integration opportunities or custom automation solutions, we welcome your inquiries.
You can contact us here: VallumADR@vallumsoftware.com